OUR SECTORS
High-Performance Materials for High-Performance Needs!
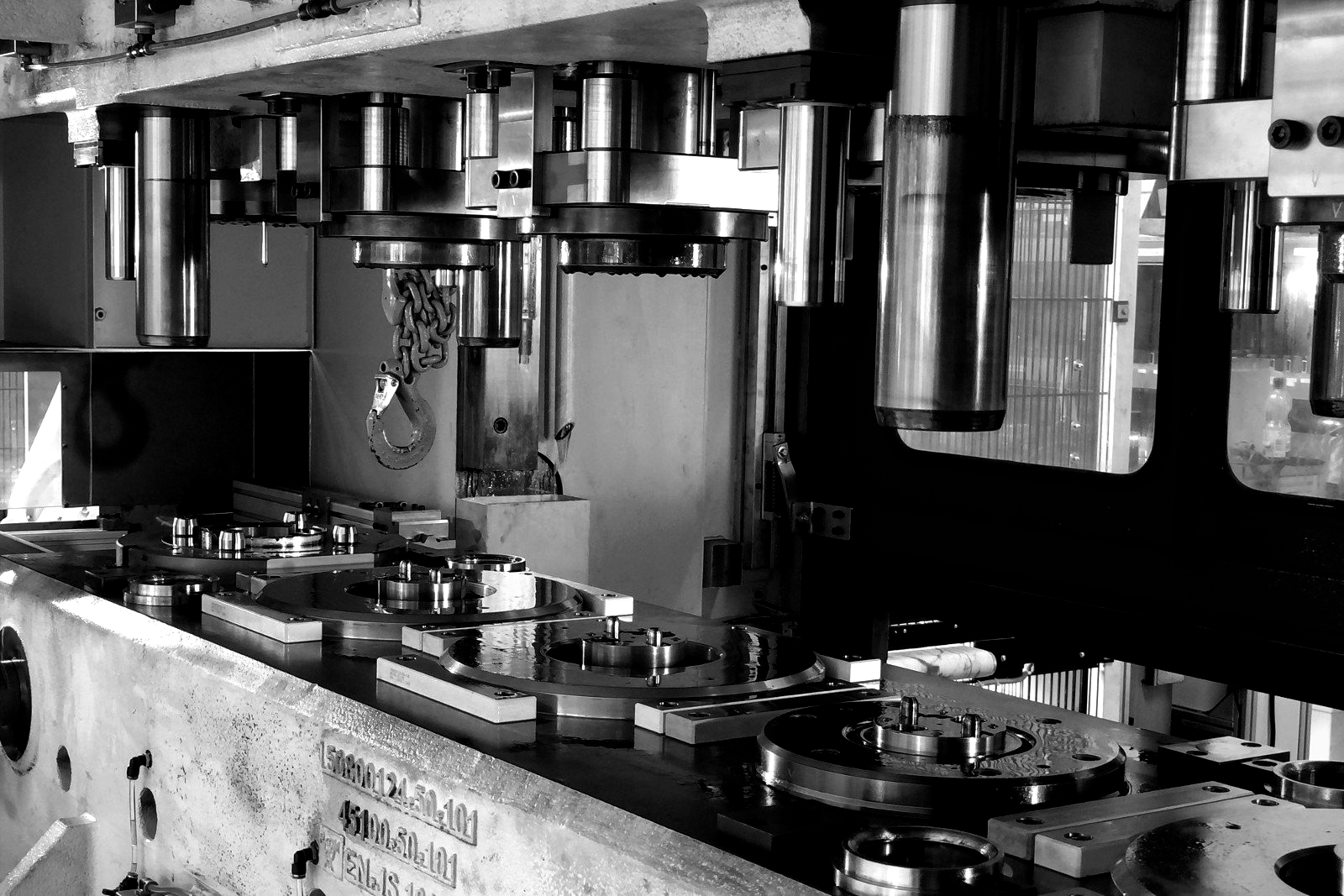
Toolmaking
Based on many years of experience in toolmaking, we know the requirements for the materials used there very well. Cutting elements such as punches or dies in individual shapes can be ideally produced additively. Embossing stamps for high-strength sheet metal materials or even special mold inserts are predestined for the use of Kolibri materials. For example, the integration of targeted lubrication in hard-to-reach places, the repair of worn components and wear resistance of up to 68 HRC are typical features of Kolibri MMC.
Mechanical and Plant Engineering
As in toolmaking, we can also draw on many years of experience in machine and special machine construction. Here, 3D printing is a flexible, cost-efficient and fast manufacturing method compared to traditional alternatives. Individual components and small series can be produced much more economically and spare parts can be obtained quickly. Wear parts can be reproduced directly on site, which creates independence from suppliers and minimizes idle times.It is not without reason that this industry is one of the largest areas of application for additive manufacturing.
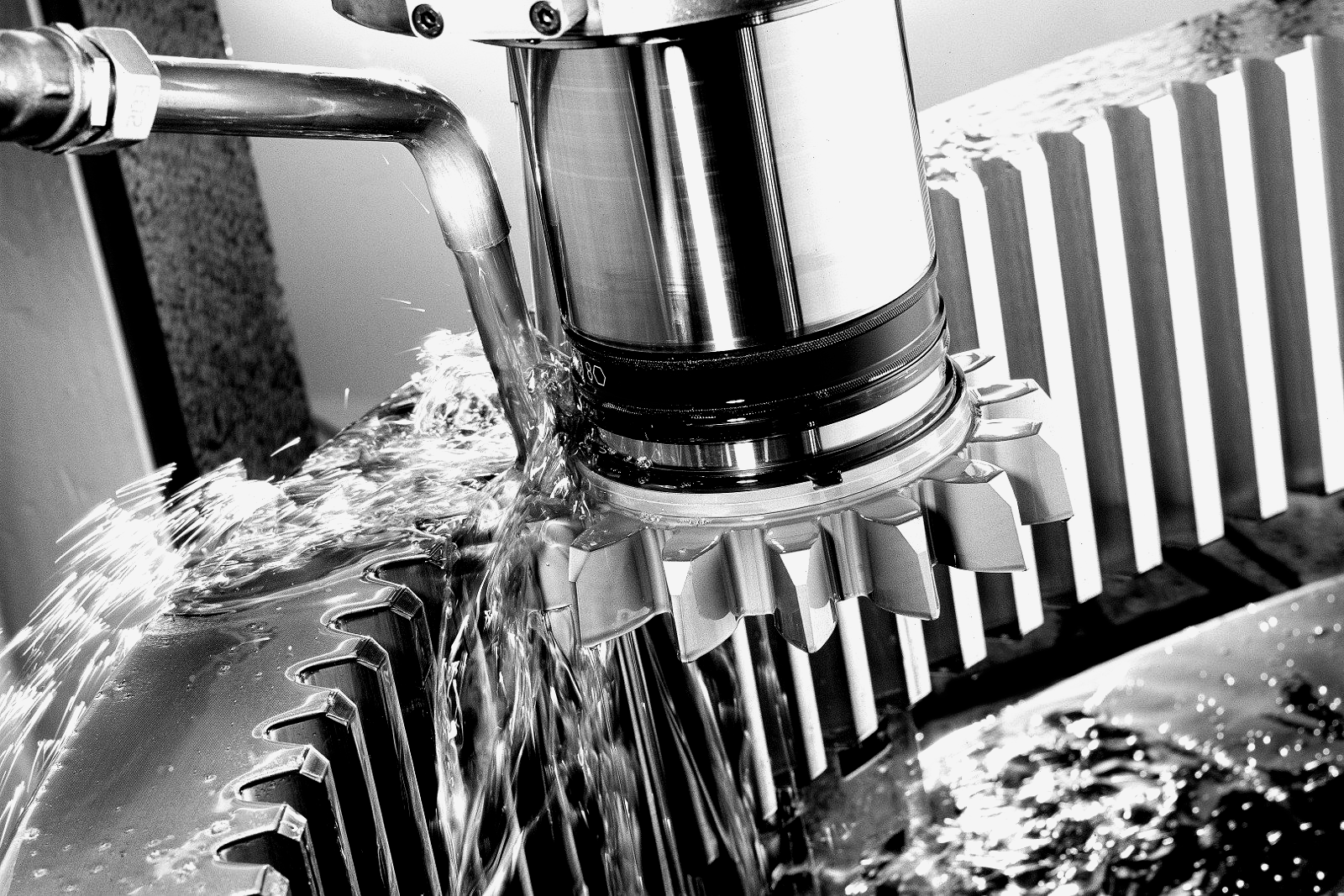
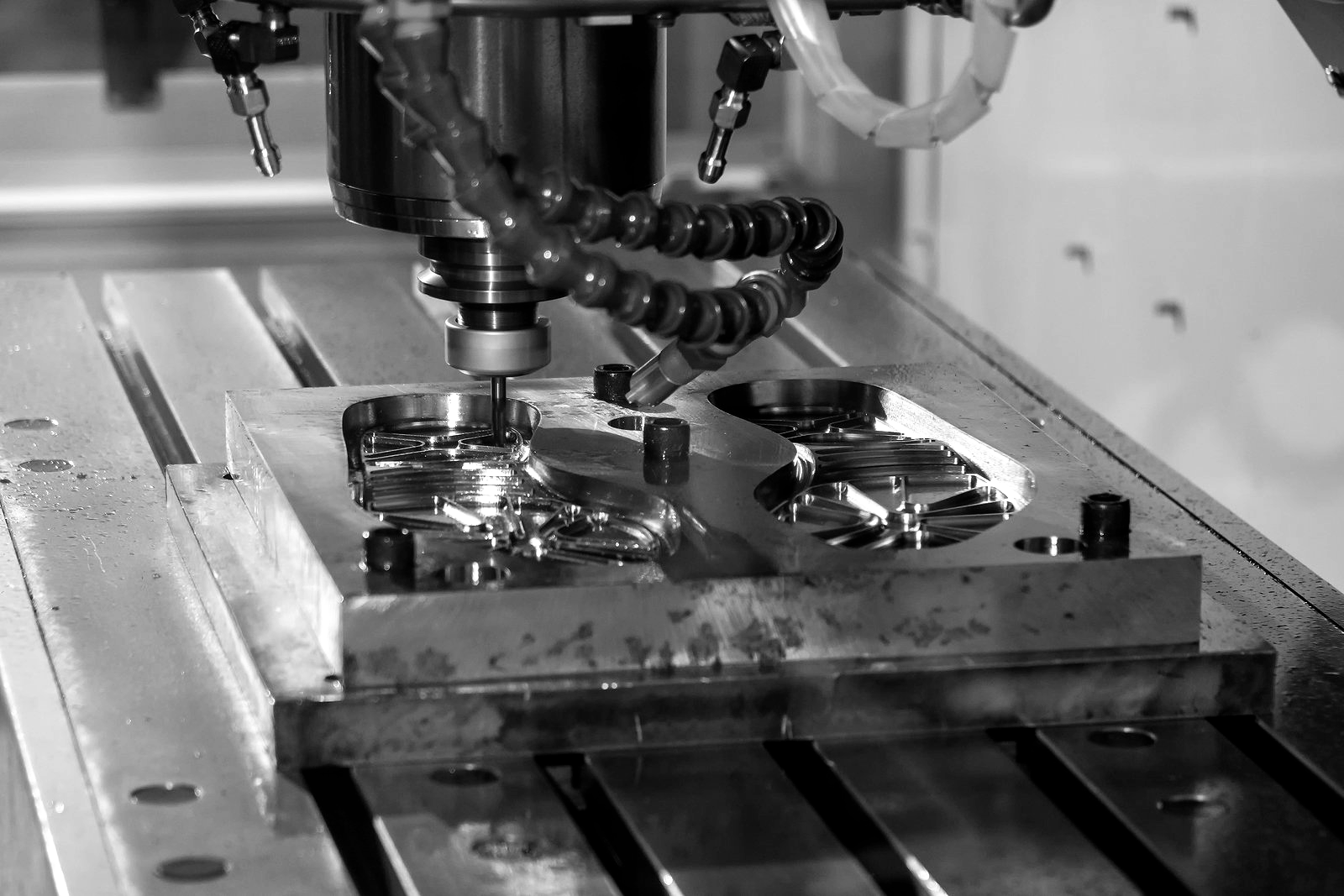
Mold Making
Mold making is one of the "first movers" in additive manufacturing. 3D printing technology has been successfully used here for many decades. Cycle time reductions of more than 30% have been achieved with near-contour mold tempering and significantly increase the productivity of a mold. Steels of grade 1.2343 and 1.2344 are frequently used. While these provide satisfactory results, Kolibri's goal is to significantly increase tool life and significantly reduce cycle times. At KOLIBRI, we are experts in 3D printing for materials with a carbon content above 0.5%.
Construction / Mining / Recycling
Entire houses can now be created in just a few hours with the help of additive manufacturing. The construction and mining industry is also an important field of application for our materials and components at KOLIBRI. The use of our materials in these industries is characterized by higher toughness and increased cutting performance compared to carbide. Perfected drill bits, hammer drill and percussion drill plates or even completely individual tools can be produced with the help of our manufacturing technology.
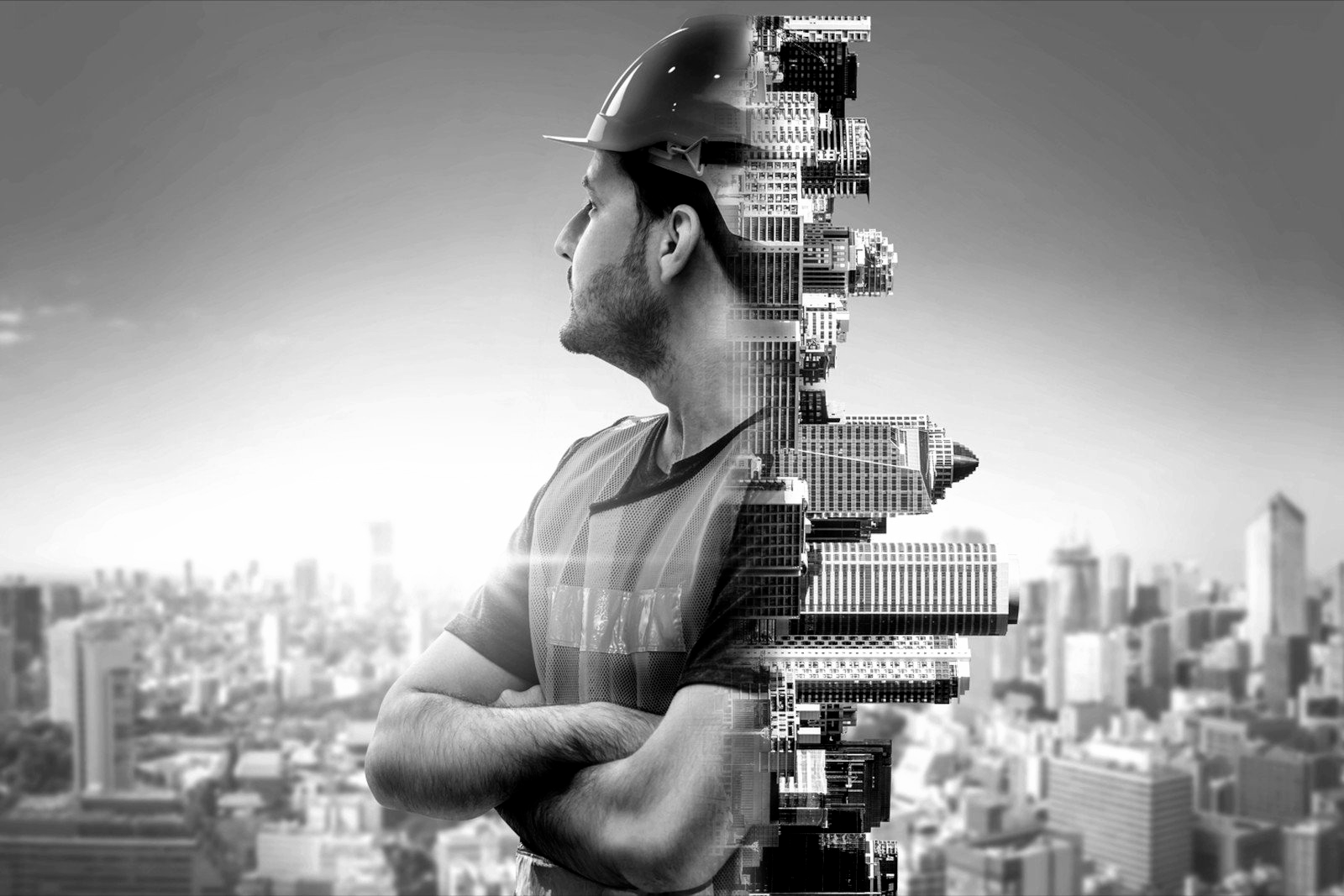
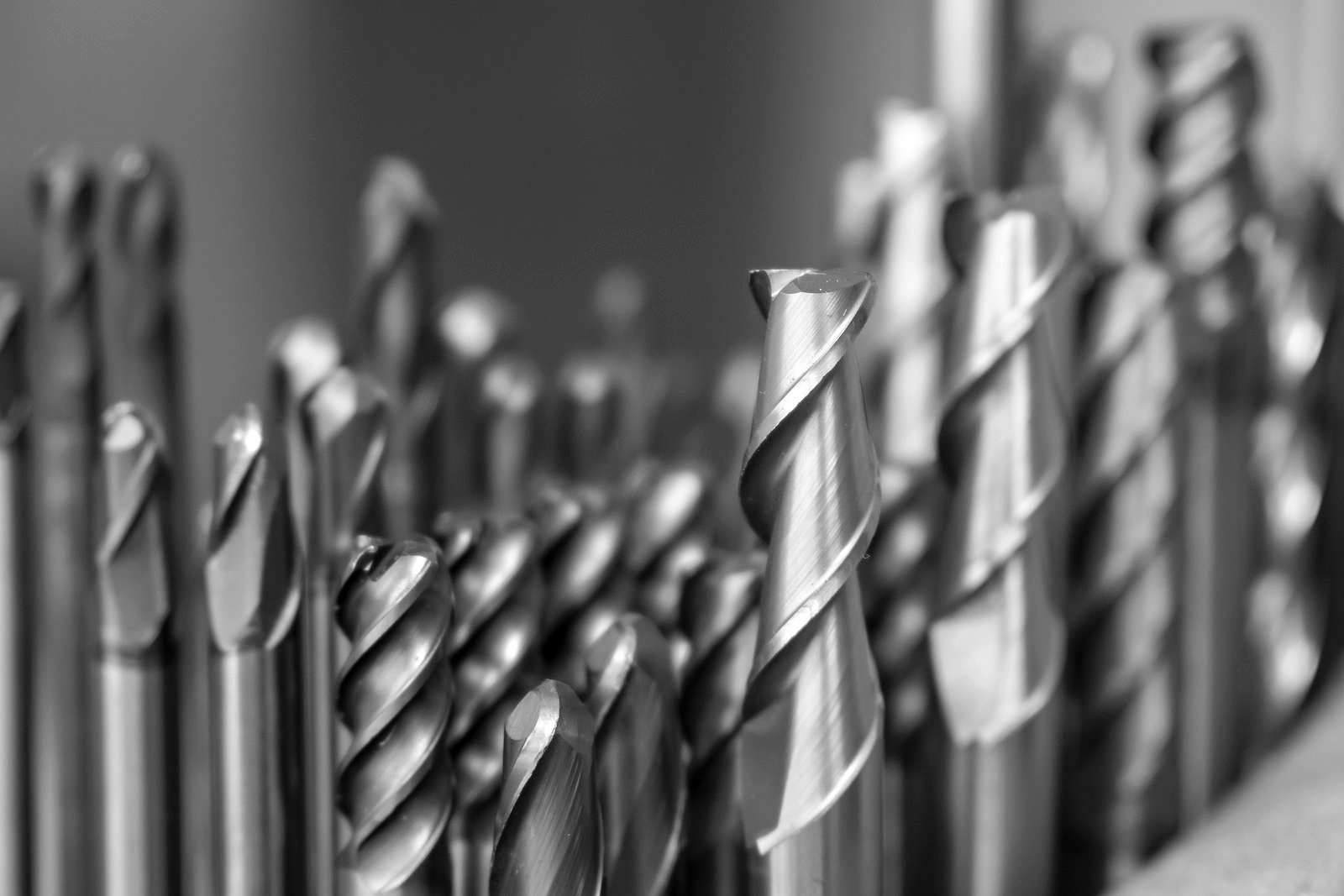
Classic subtractive manufacturing processes are predominantly used in metal and wood processing. Kolibri stands for near-net-shape production of blanks made of high-speed steel, MMC-designed cutting materials, integrated cooling channels, tougher material for increased service life and application-specific design with complex geometries.
Food & Pharmacy Industry
Acidic materials or abrasive particles are often a major nuisance for the industrial engineering departments of pharmaceutical and food manufacturers. These attack the surface of stainless steel lines, tools or switching units. At Kolibri, we make it possible to reduce the individual components and to design tools or components in such a way that wear and tear is reduced, thus increasing freedom from maintenance.
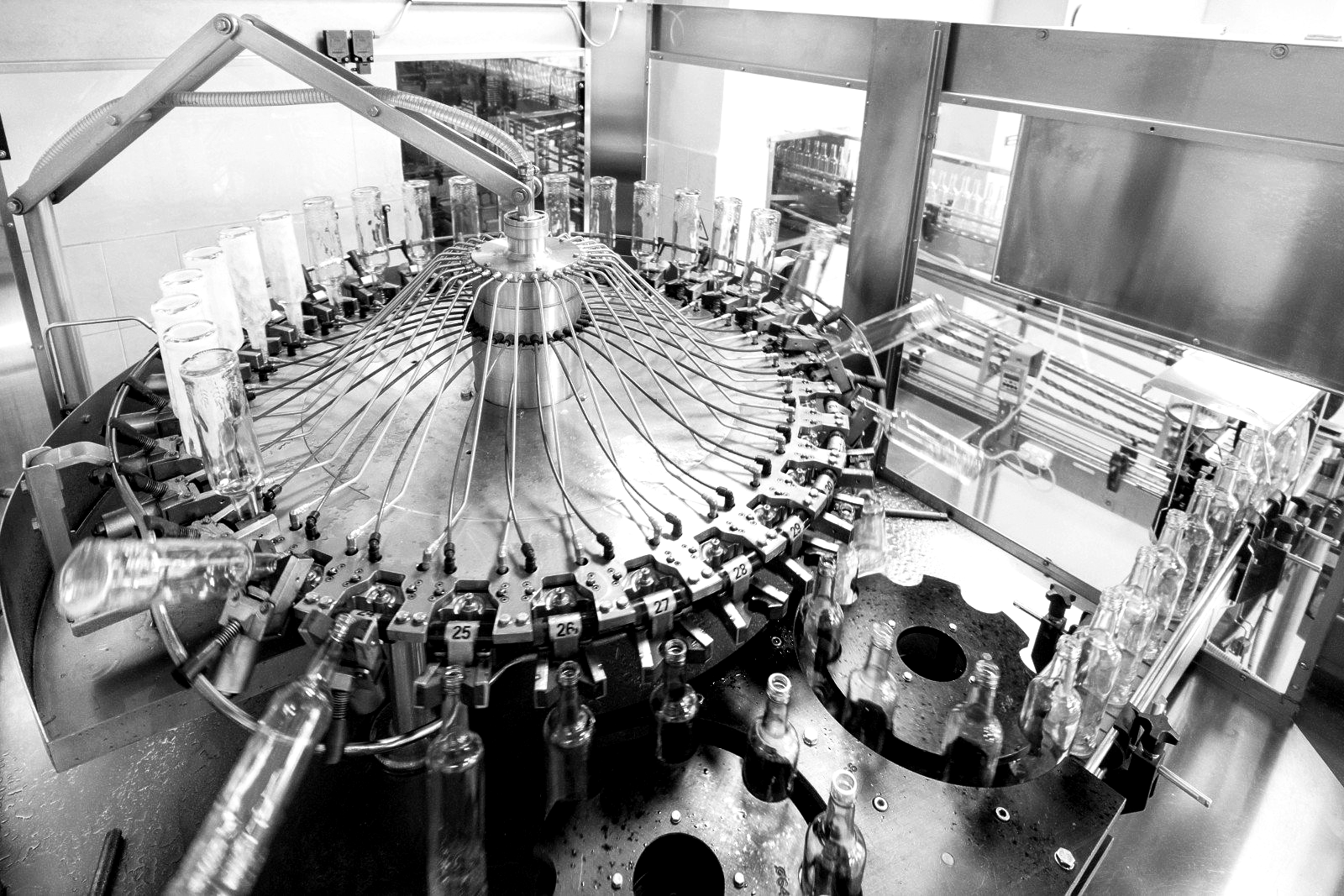
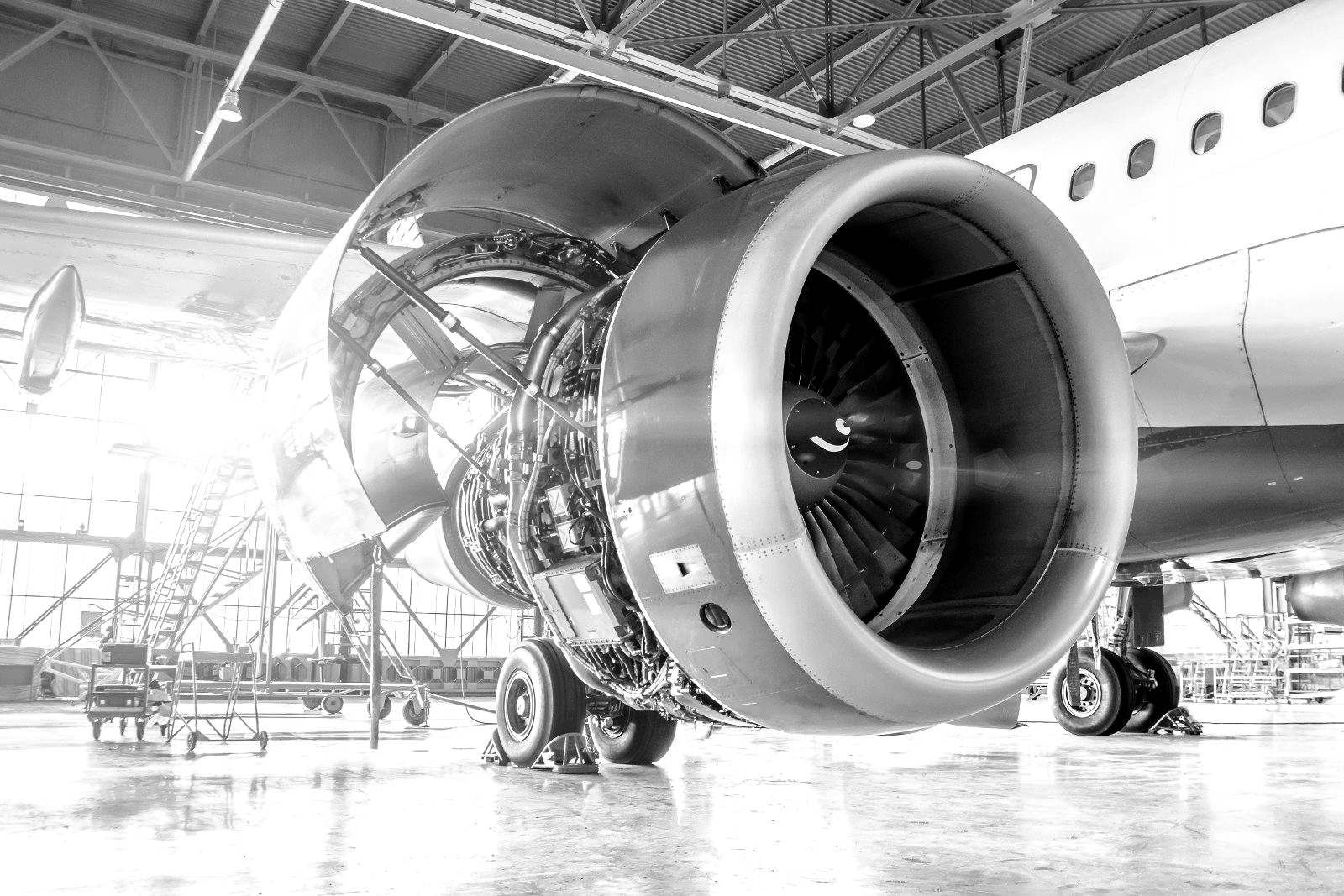
Aerospace Industry
3D printing has been a standard process in the aerospace industry for decades. With the help of additive manufacturing, it is possible to meet the particularly high requirements in terms of precision, complexity, safety and weight. Kolibri can support the production of high-quality lightweight components with its knowledge. Whether in the area of wear or weight reduction of high-strength components - Kolibri can provide valuable assistance with its material compositions.
Medical Industry
The medical and dental technology sector is one of the pioneering sectors of 3D printing. Additive manufacturing has already established itself successfully and marketably, especially in the areas of dental, medical and hearing aid technology as well as prosthetics and in the manufacture of medical aids. The advantages are obvious: Implants, prostheses and dentures, for example, which were previously only available in different standard sizes, can be individually adapted to the patient with millimeter precision. High-strength MMC can improve the quality of life of the patients, simplify the surgical procedure and sometimes avoid the second procedure.
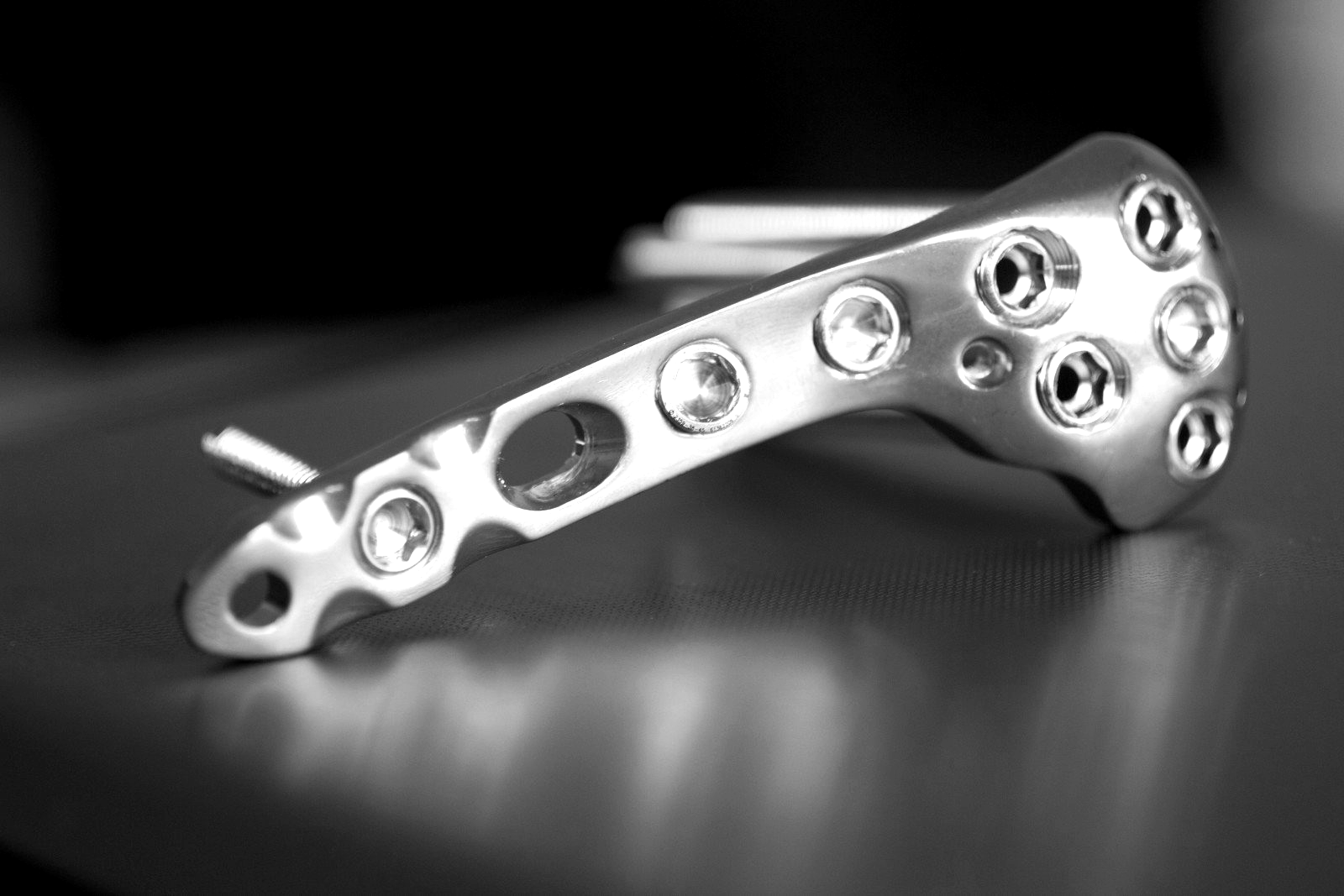
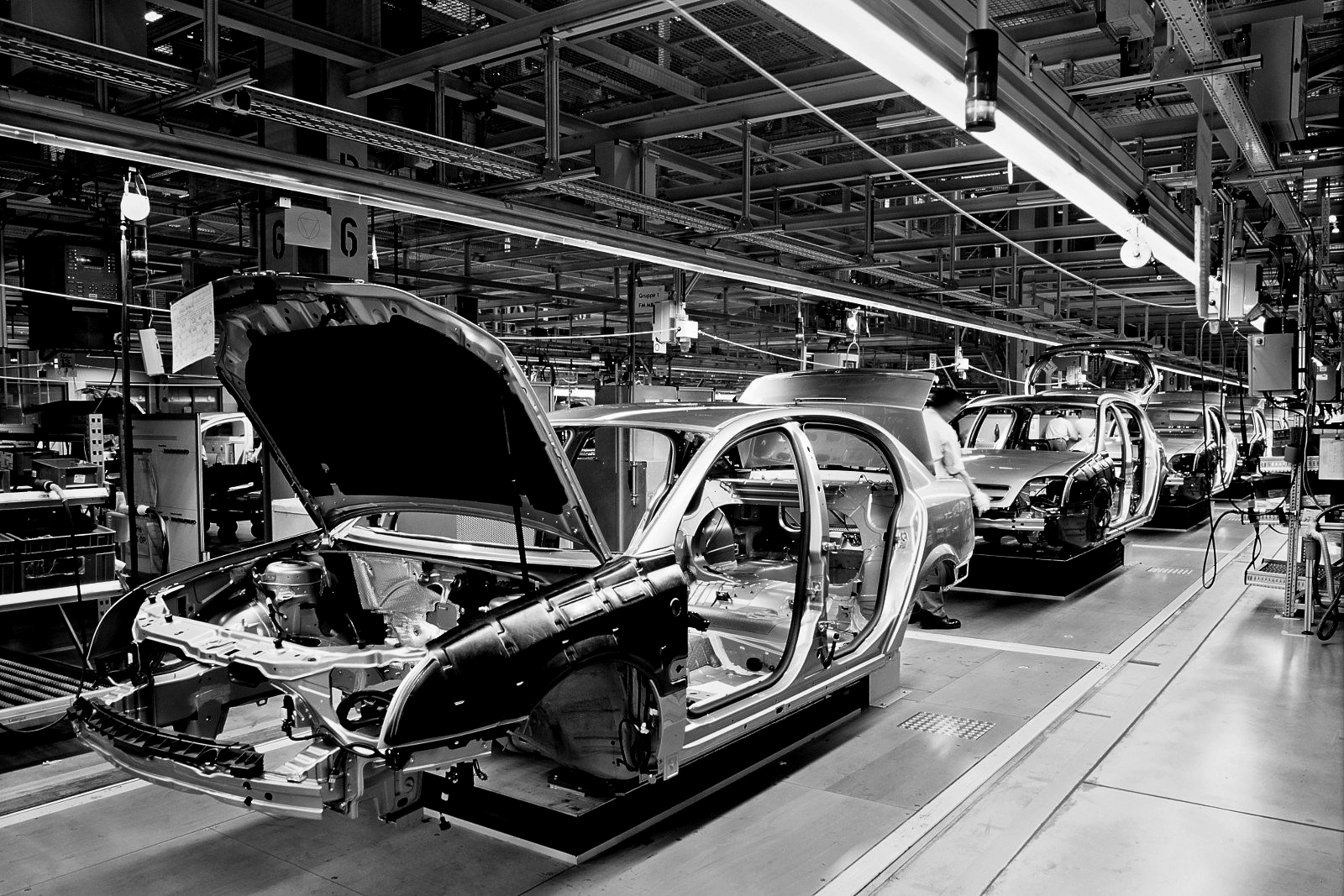
Automotive Industry
3D printers are now part of the standard manufacturing equipment in the automotive industry. Additive manufacturing processes are slowly gaining a foothold in serial production and are not only used for the production of spare parts for classic cars or the creation of prototypes. Above all, the 3D printing of tools and devices that support the manufacturing process offers significant added value for automobile manufacturers. Kolibri is already leading its contribution to progress here.